Custom mixed steel, and precise
control of the heat treating process are the keys to
Bondhus having the highest quality tools on the market.
Protanium® high torque steel is much more than just
steel and much more than just a name. It’s a
specification, it’s a process, and it’s a commitment to
a level of quality unmatched by any competitor.
The Bondhus approach to producing Protanium® Steel is a
six step process producing results that consistently
blow the competition away in tests conducted for
hardness, ductility, quality, wear, consistency, and
support.
Custom steel Bondhus
has achieved the greatest strength, hardness and durability
of any hex tool manufactured in the world. Only Bondhus uses
custom mixed steel. A variety of lower quality steels are used
by other manufacturers. Chrome vanadium, 1050
carbon steel, S2, and 8650 are examples of common alloys
in use.
|
Steel considerations:
- Protanium® Steel is proprietary alloy steel
developed and used only by Bondhus. It is the
hardest, most ductile, and longest wearing steel
that exists in the hex tool industry. Bondhus
uses Protanium® Steel on all of its standard
tools.
- 8650 is the most common steel alloy in use
throughout the U.S. and the Far East. It does
not have the hardness or ductility of Protanium®
Steel.
- Chrome Vanadium is comparable in quality to
8650, and often used in Europe.
- Chrome Moly is similar to Chrome Vanadium, but
is, however, stronger and harder. Because it is
fairly expensive, manufacturers generally only
use it on their higher quality and higher priced
tools like ball head products. They often
substitute lower grade alloys for their other
tools. Europe and Japan are the primary users.
- S2 is used by only a small number of
manufacturers. It is harder than 8650, but it is
also less ductile, and far more prone to
shattering.
- 1050 carbon steel is a low grade steel that is
inferior to those listed above, but is still
used by some manufacturers in Europe and Asia.
|
Bondhus advantages:
- Bondhus uses proprietary Protanium® Steel, not common
alloys such as 8650.
- The hardness values of up to 60 RC
(and above) achieved by Bondhus tools are unattainable
with lower grades of steel.
- Bondhus tools also achieve the highest degree of ductility
and durability in the industry.
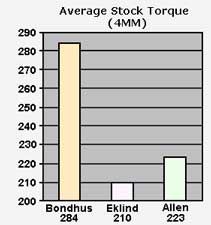
|
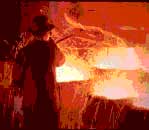
Protanium® Steel
is not an 8650 grade steel, it is not a form of
S2, and it is not a grade used by any other
manufacturer. It is created with a formula known only to
Bondhus – a formula that is the result of many years of
research and improvement of the specification. With the
addition of elements like chromium, nickel, molybdenum,
manganese, silicone, and vanadium, Bondhus controls more
of the elements in the steel mixture, and more precisely
controls the heat treating of each batch, than any other
competitor in the market.
Education of suppliers
Bondhus personally visits and works extensively with
steel mills and drawing mills in the production of
Protanium® Steel. Every mill must not only be taught the
process, but agree to conform to the entire standard.
Meticulous quality control, testing, and documentation
are something that only a select few mills are willing
to commit to.
|
Vacuum degassing or Argon bubbling
With the exception of Protanium® Steel, removing hydrogen is done by
simply allowing steel to cool slowly. That is not an effective solution,
however, because hydrogen forms high pressure pockets
within the steel and compromises its integrity.
Vacuum degassing or argon bubbling is the solution to
the problem of trapped hydrogen. Cleanliness is also
improved, because the removal of alumina has the affect
of producing very clean steels.
With so many benefits, why don’t our competitors use the
technique? The answer is twofold. Cost is the first
factor, and the second is the fact that not all mills
are even capable of performing the task.
Bondhus is the only hex tool maker that goes to the
extreme of performing this all important step.
|